The compact drive and positioning inverter saves on space and reduces the complexity of your systems. Thanks to decentralized technology, it has a high level of integration and can replace entire control cabinets in the field.
Decentralized drive inverter with positioning control makes project planning easier
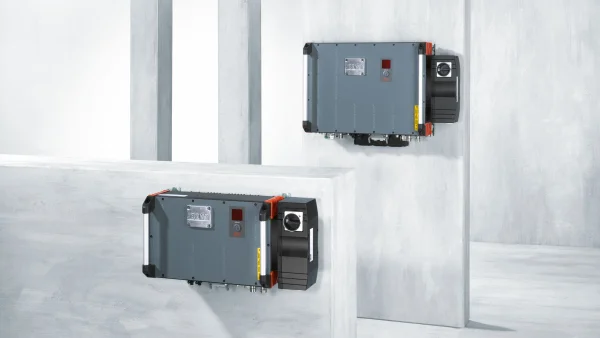
Do you want to significantly reduce the complexity of your system architecture? Are you looking for a practice-oriented drive solution that takes up little space and is resistant to vibration?
In that case, the MOVIPRO® SDC drive inverter with positioning control from our decentralized drive technology portfolio is the right choice for you. The compact unit provides a high level of integration and can replace entire inverter control cabinets in the field. It also has the advantage that the controller is located near the drive.
In this way, you can install autonomous drive sectors and network them with the MOVIPRO® SDC. Depending on your regional requirements, communication is possible via all common bus systems: PROFIBUS, PROFINET, DeviceNet, EtherNET/IP and MODBUS/TCP.
Conveyor systems and machines that have consistent, decentralized drive technology such as this are far superior to comparable centrally-controlled systems.
MOVIPRO® SDC is therefore the best drive solution for you:
Standardized 1-axis application modules make project planning significantly easier for you. You can use them to implement speed control and positioning commands conveniently, simply and quickly at any time. There is also no need for programming because parameterization is performed by the user.
The standard control technology also ensures consistency within your system, as the flexible, field-oriented inverter can control both asynchronous and synchronous motors. Furthermore, the inverter includes local I/Os and supports various brake voltages.
Create the basis for open and flexible system architecture with the MOVIPRO® SDC drive and positioning controller. Regardless of whether you are designing a new system or modernizing an old one, functional compatibility with existing control cabinet applications is guaranteed. When combined with our MOVITOOLS® MotionStudio you can benefit from an integrated software environment for your entire engineering process – from startup and diagnostics right through to maintenance.
- If vast installations need to be equipped with and automated by electrical drives
- If your system is based on reusable modular functions
- If your process requires a compact and integrated drive controller
- If you want to implement optimal speed control and precise positioning
- If you plan to manage I/Os and encoders locally
- If quick diagnostics and maintenance are important to you
- If you want a complete drive solution in one package
Configure your individual product
- Detailed information about your individual product
- Option to directly request a quotation or place an order
- CAD data and documentation for your configuration
Your benefits
-
Convenient control
via the simple user-defined parameterization without the need for programming and via standardized 1-axis application modules. -
Perfect networking
due to the high level of integration and communication across all common bus systems. -
Reduction in idling time
thanks to decentralized engineering and easy connectivity, allowing quick retrofitting of systems and a reduction in wiring errors. -
Increased consistency
thanks an integrated installation concept for the entire materials handling technology. Same software tools for operation/diagnostics. -
Reduction in complexity
thanks to communication via common fieldbus systems and support for a wide range of motors (asynchronous and synchronous).
Features
- Speed control and positioning
- Optional encoder feedback for motors and tracks
- Integrated brake control with different brake voltages
- Fieldbus interfaces: PROFIBUS, PROFINET, PROFIsafe, EtherNet/IP, Modbus/TCP, DeviceNet
- Integrated digital inputs and outputs
- Optional RS485, SBus, SBusPLUS interfaces for external actuators and sensors
- Plug-in interfaces for energy, motors (power), and encoders (signals)
- Local memory for parameters
- IP54 degree of protection
- Robust aluminum housing
- Optional maintenance switch
- Optional, separable connection unit for linear power bus
- Safe Torque Off (STO) up to PL d according to EN ISO 13849-1
- Optional: Safe PROFIsafe bus system
Technical data
- Power range 2.2 to 15 kW
- Size BG0: 2.2 kW
- Size BG1: 4 kW, 7.5 kW
- Size BG2: 11 kW, 15 kW/operation without fan up to 11 kW
- 12 DI + 4 DIO (DI=digital in, DIO=digital in/out)
Areas of application
Use of MOVIPRO® SDC application inverter for decentralized system designs
For consistently defined, decentralized drive solutions, MOVIPRO® SDC focuses primarily on conveyor and machine applications in the automotive industry, production logistics, and intralogistics:
- Scissor lift tables
- Lifting/lowering conveyors
- Lifting stations with lift tables
- Conveyor trolleys
- Feeder conveyors
- Rotary distributors
- Rotary tables
- High-speed horizontal conveyors with positioning
- Transfer systems on rails
Accessories
Accessories for convenient handling
- Interface box for convenient connection to power supply
- Terminals for daisy chaining connected voltages
- Integrated maintenance switch for disconnecting the MOVIPRO® from the supply system for service purposes
- Size BG2: 11 kW, 15 kW/operation without fan up to 11 kW
- Sensor/actuator box for connecting up to 8 sensors or actuators:
- Connection cable with M23 plug connector, and M12 slots for sensors or actuators
- 2 LEDs for each M12 slot for status display
- with connection cable lengths varying from 1 m to 10 m
- External braking resistors for applications with 4Q drive operating mode for dissipating regenerative power to MOVIPRO®
- STO jumper plug for deactivating MOVIPRO® safety functions, if required
- Mounting accessories: Handles and external mounting bracket
- Fan components for MOVIPRO® ADC size BG 2, 11 kW (fan groups are obligatory for 15 kW and are pre-assembled)